
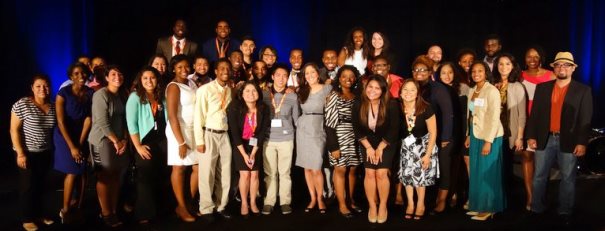
For precise positioning of RUNTs on the surface, the important parameters in the roll-up process are the sacrificial layer thickness, etching time, and tube diameter.
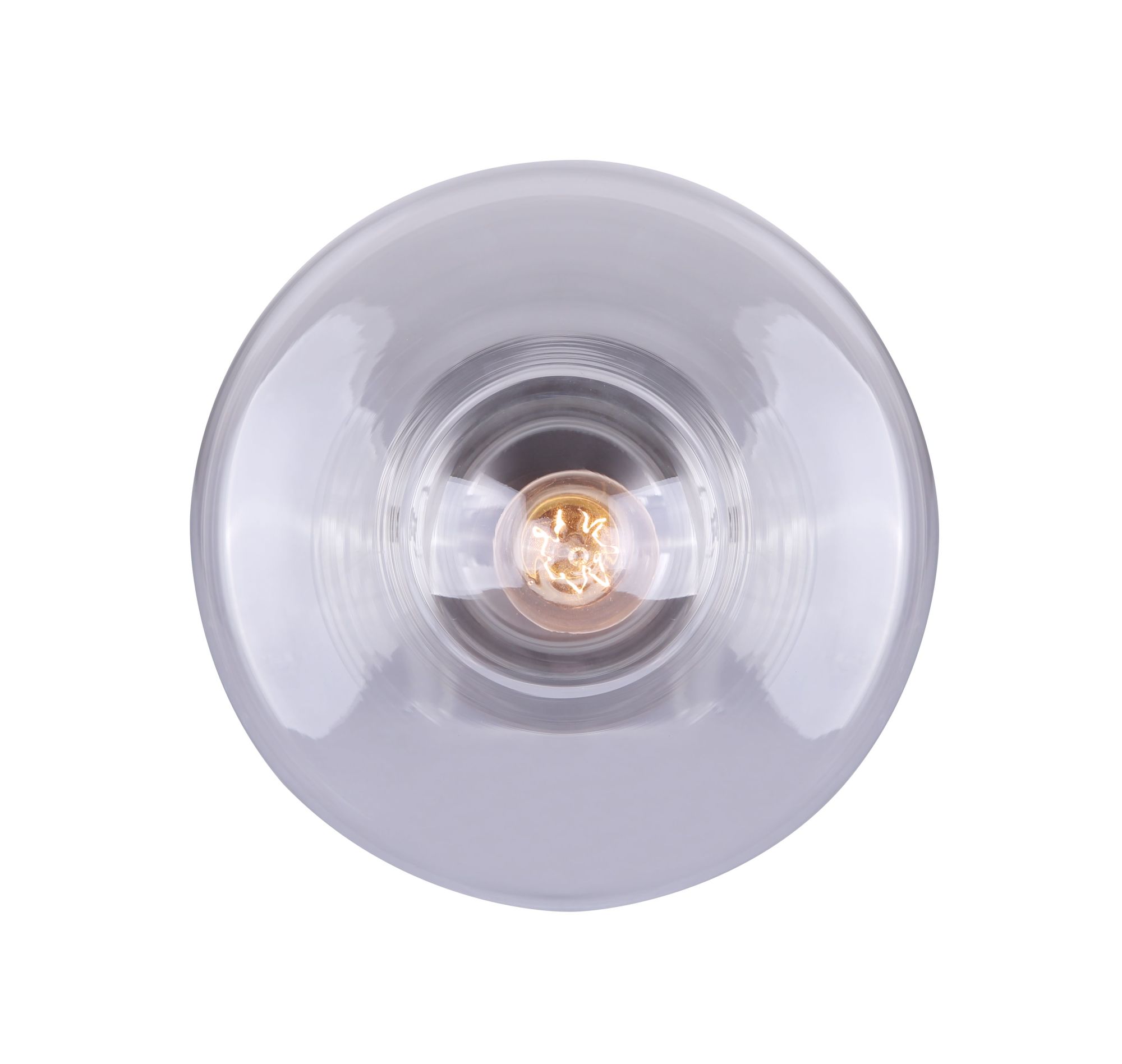
The tube diameter, i.e., the size of the cross section of the structure obtained after the etching step has been completed, depends on the thickness and inherent strain of the layers, and can be accurately varied in the nano- to micrometer range. The starting edge, which for InGaAs/GaAs layers should be oriented in the direction for optimal structural integrity of the resulting RUNTs, can be defined either by scratching the surface, thereby laterally exposing the sacrificial layer, or by opening a window through the entire layer structure by photolithography and subsequent wet chemical etching.
Illuminate kipp full#
Finally, the bent bilayer forms a tube or scroll after performing a full rotation. The aim of this study was to quantify the observed “etch-suppression effect” (ESE) and precisely control the release of InGaAs/GaAs bilayers with an illumination technique.įigure 1a shows schematically the formation process of a III–V rolled-up nanotube (RUNT): when immersed in HF solution, the compressively strained double layer (a GaAs layer on top of a larger-lattice constant In xGa 1− x As layer deposited pseudomorphically on a GaAs substrate with an AlAs sacrificial layer) releases from the substrate as the sacrificial layer is preferentially removed by the HF at a previously defined starting edge and begins to roll up in order to relax the built-in strain gradient. This method allows for control over the roll-up stopping point and is suitable for very thin sacrificial layers. Sufficiently intense light exposure of a certain substrate area leads to a complete suppression of the underetching effect, and as a result, the formation of rolled-up InGaAs/GaAs tubes can be easily controlled spatially. Here, we demonstrate illumination-controlled hydrofluoric acid (HF) etching of a buried thin AlAs sacrificial layer. Numerous existing studies offer highly sophisticated methods for precise lateral positioning of rolled-up semiconductor nanostructures by controlling the starting edges, but difficulties arise for thin layers due to the extensive, successive lithography steps involved, and ways to control the stopping point of rolling remain largely lacking without modifying the structure. Precise control over the lateral positioning and the number of windings is fundamental for the use of the tubes in optical resonators for sensors, hyperlenses, or electrical transport (curved electron gases). However, in some cases, it might be important to stimulate tube formation in certain areas and suppress tube formation outside those areas.
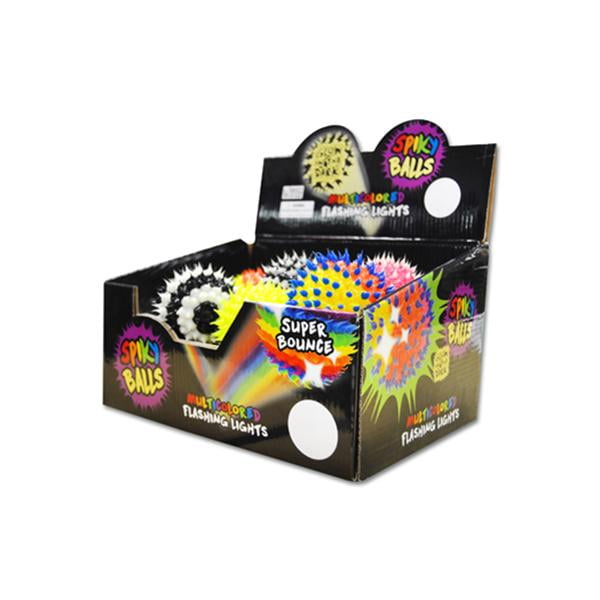
Large arrays of periodically ordered microtubes can be fabricated by a combination of lithography and deliberate self-rolling of strained layers upon selective underetching. Rolled-up nanotech has become a powerful technology with applications in a broad range of research fields, including optofluidics, micromachinery, magnetofluidics, biophysics, nanomechanics, and waveguiding for different spectral ranges and applications.
